How to make fiberglass rods?
At Discount Stake, we are dedicated to custom fiberglass pultrusions, and offer the right product at the right time for the right price.
Unlike most FRP molders, Discount Stake uses a pultrusion process to manufacture Fiberglass Products. This is important, because it means we can use many more resins and reinforcements, each adding unique and desirable properties to the final product.
Through pultrusion, Discount Stake can deliver:
★ Stronger and more reinforced components, with greater tension strength and rigidity than you’ll find in regular FRP molded products
★ Profile shapes that can’t be achieved through regular FRP processes
★ Larger products (owing to the fact that pultrusion creates a continuous flow of FRP).
Ultimately, through Discount Stake you get a superior strength and precisely tailored product which better meets your design criteria.
Pultrusion is a process for converting reinforced fibers and resin into fiber-reinforced plastic (FRP). The resulting FRP is tough, light, and extremely versatile.
What’s Pultrusion?
Pultrusion is a manufacturing process for converting reinforced fibers and liquid resin into a fiber-reinforced plastic, also known as fiber-reinforced polymer (FRP).
The pultrusion process allows the continuous production of FRP structural shapes in an automated, energy-efficient process by pulling fiberglass rovings through a resin bath or resin impregnator that completely saturates the reinforcements. The resin hardens from the heated steel pultrusion die, resulting in a strong, lightweight final product that follows the shape of the die.
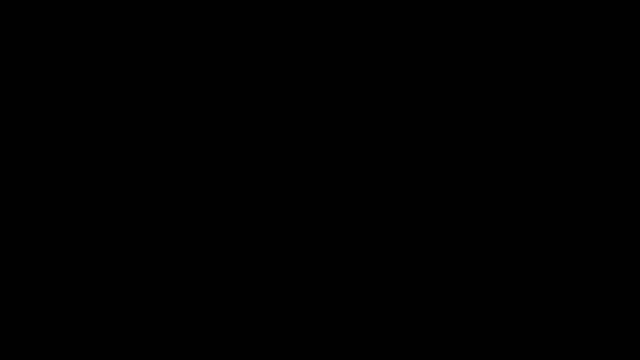
Pultrusion Process
Pultrusion machine design can vary as part geometry can differ. The two main types of pulling systems used to create FRP profiles are reciprocating (hand-over-hand) and continuous (cat-track).
The rovings of fiber reinforcements are positioned by the creels for continuous feeding onto the guide plate. To ensure strength and quality, the fiber reinforcements must be positioned accurately within the finished composite.
The resin impregnator is optimally designed to completely saturate the fiber reinforcements in a resin bath or wet out that consists of either epoxy, polyurethane, polyester or vinyl ester. Fillers and other additives such as colors, fire inhibitors and UV retardants can be included to improve the lasting performance of the composite.
As the reinforcements exit the resin impregnator, they’re passed through “pre former” tools, designed to squeeze out surplus resin and organize the fiber reinforcements into the correct shape. During this process, additives such as continuous strand materials and protective surface veils are often included to improve the structure, resistance to corrosion and finish of the final product.
After this process, the resin-impregnated fiber passes through the steel die for polymerization. The die is heated at a consistent temperature to cure the thermosetting resin, resulting in a solidified polymer.
The Unique Properties of Pultruded Fiberglass
A few crucial attributes make FRP unique and valuable as a manufacturing material.
Fiberglass FRP is Light and Strong
Pultruded fiberglass is a lightweight material, weighing around 30 percent less than aluminum and 70 percent less than steel. However, it can also be comparable in strength to steel and is significantly less prone to deformation under impact than commonly-used metallic manufacturing materials.
The combined lightness and strength of FRP delivers obvious manufacturing advantages for a wide range of products. This attribute also means that working with the pultruded products is frequently safer, and will require less heavy equipment than would typically be required for manufacturing materials like steel or wood.
It Won’t Conduct Heat or Electricity
Fiberglass FRP is an ideal material for creating a protective barrier between hot or electrically charged components and the end user. Steel and aluminum will readily conduct both heat and electricity. Pultruded fiberglass will not.
Pultruded fiberglass therefore has a wide range of applications for making products safer to handle, including protective sheathing for metallic components, tool handles or component casings.
Fiberglass FRP is Corrosion Resistant
Pultruded fiberglass won’t rot. Nor will it be compromised by invasive pests or gradually degrade when exposed to moisture, temperature extremes or UV radiation from the sun. Its extreme resilience makes pultruded fiberglass ideal for outdoor applications, particularly where the material is likely to be in direct contact with the elements.
Another clear win from using FRP is that it requires far less maintenance than organic materials like wood or rust-prone materials like iron or steel.
It’s Extremely Versatile
Fiberglass FRP is one of the most versatile manufacturing materials. It can be fabricated into a vast array of shapes and profiles including tubing, rods, sheets and customized shapes. Moreover, this shaping can be done inexpensively in comparison to wood, aluminum or steel. This versatility means FRP is often a superior choice for highly-customized or intricate components.
Using custom dies, Discount Stake can create profile shapes of almost any configuration, and can work with you to build components with specifications that precisely fit your design concept. We can greatly extend your manufacturing reach with new possibilities for industrial design.